L'appareil, comprenant un nœud de plasma et une source d'alimentation, peut fonctionner selon un régime spécial de décharge magnétron: la pulvérisation se produit en même temps que l'évaporation intensive de matériel fondu qui forme la couverture. D'après l'article des chercheurs publié dans la revue Surface and Coatings Technologies, cette nouvelle technologie permettra de créer rapidement et efficacement des couches fines demandées dans les domaines technologiques de pointe.
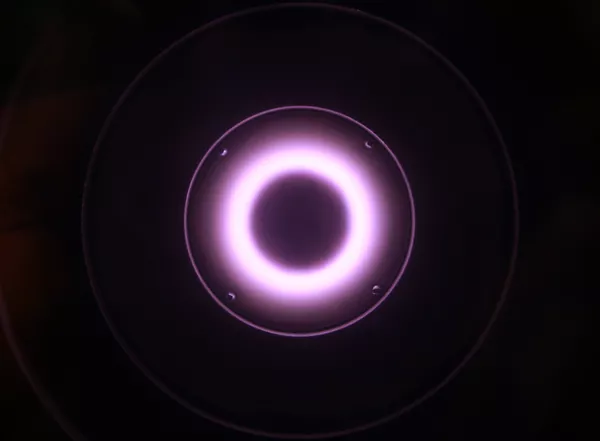
L'application magnétron représente une part très importante du marché de la production de couvertures métalliques et diélectriques destinées à l'électronique, à la construction mécanique, à l'architecture et à d'autres secteurs. C'est par exemple le seul moyen permettant d'appliquer une couche conservatrice d'énergie sur les vitres des bâtiments. Qui plus est, cette méthode sert à créer des couches dures sur des outils tranchants, ainsi que des couvertures décoratives — par exemple pour appliquer du nitrure de titane sur les dômes des églises au lieu de l'or. On l'utilise également pour métalliser les plaques des circuits intégrés dans le domaine de la microélectronique ou pour créer des filtres dans l'industrie optique.
"La pulvérisation magnétron conserve un problème: la formation lente des couches sur la surface des détails par rapport, par exemple, à la méthode d'évaporation sous vide", explique Alexandre Toumarkine, ingénieur du MEPhI. D'après lui, la qualité des couvertures créées à l'aide de l'évaporation sous vide est pourtant considérablement inférieure à celles appliquées par décharge magnétron. Les industriels étaient depuis longtemps face à un dilemme: soit la qualité des produits, soit la productivité de l'entreprise. "Cet appareil visant à créer une décharge magnétron pulsé avec une cathode fondue a réussi à réunir les meilleures caractéristiques des deux technologies", affirme le chercheur, soulignant le potentiel technologique énorme de cette méthode.